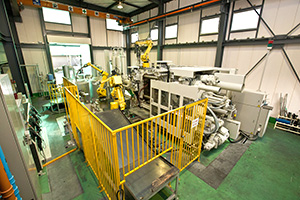
Special features of our semi-solidification casting (nanocasting) method
- Because the molten aluminum passes through a semi-solidified stage, its metallographic (granular) structure remains stable.
- Compared with an ordinary die-casting method, the temperature is lower and viscosity is higher, so fewer shrinkage cavities and gas pockets are formed and dimensional accuracy is improved.
- During the nanocasting process, electromagnetic mixing causes the molten aluminum to cool rapidly into a semi-solidified state. This creates an extremely fine metallographic structure.
These features ensure consistently superior mechanical (tensile) properties.
Appearance of knife-cut semi-solidified slurry
Semi-solidified slurry has been removed when its condition contains both solid phase and liquid phase parts. Then it is cut with a knife.
The video clearly shows the characteristics of semi-solidified slurry.
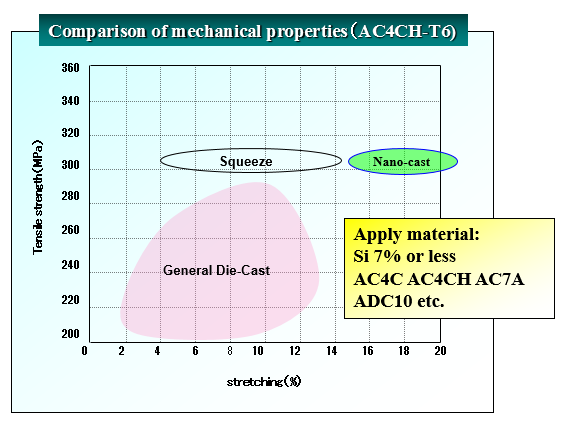
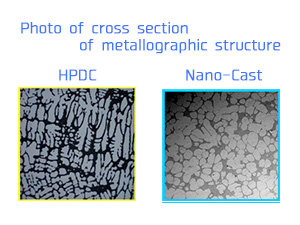
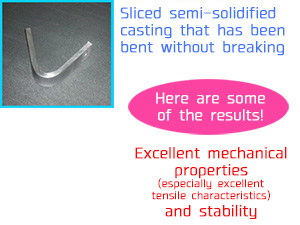
Reasons for semi-solidification (nanocasting) process
- To manufacture components that require high pressure resistance and high strength characteristics
- To use alternate materials and processes that replace cast iron and pressed components (to reduce weight)
- To use alternate processes that replace aluminum casting (to reduce cost)
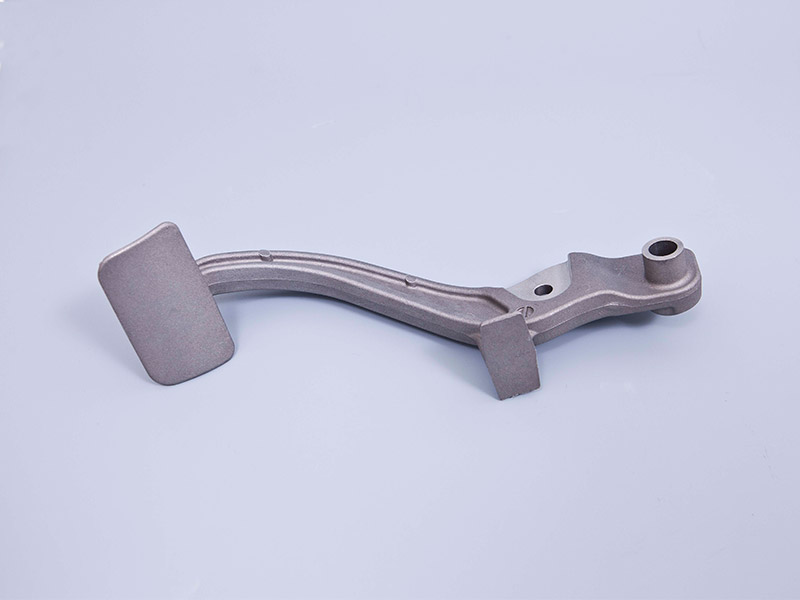
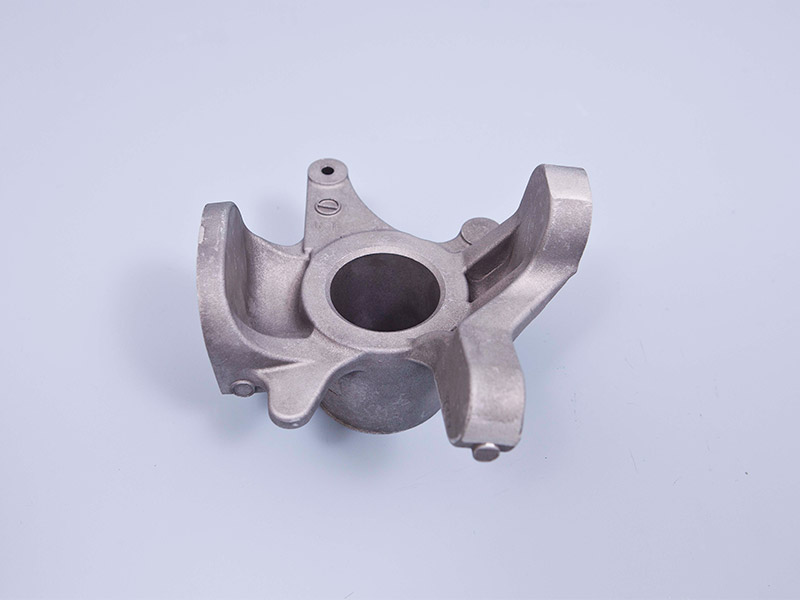
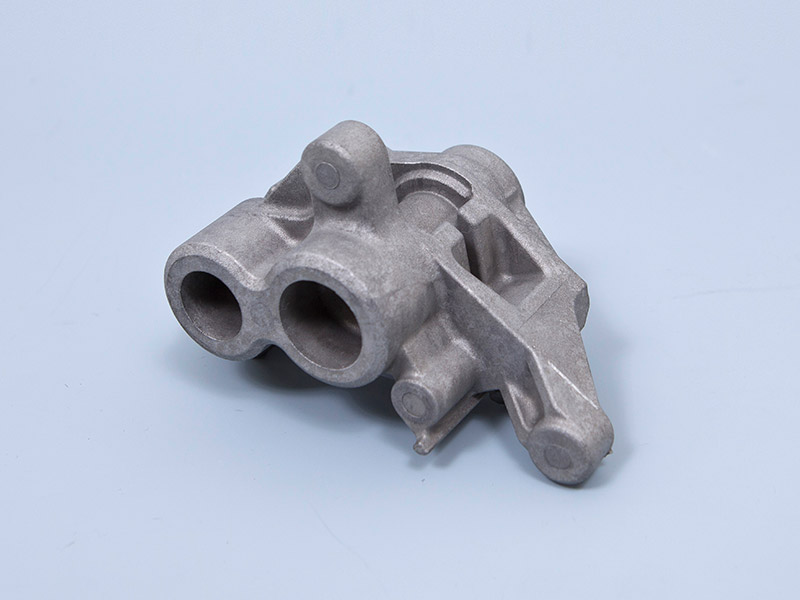