Special features of our squeeze casting method
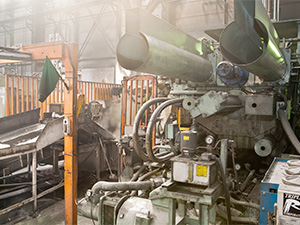
- Machine direction injection permits slower fill casting
- High pressure casting (approx. 1 ton)
- Directional solidification (solidification starts at the top and ends at the gate)
These features reduce gas pockets caused by gas entrainment while also reducing shrinkage cavities.
At Reterra, mold closing is accomplished through horizontal clamping, as it is with a conventional die-casting machine, while the molten metal is injected from below toward the upper part. This method is the best for maintaining the temperature of the molten metal and for ejecting air.
Low pressure die-casting and squeeze die-casting: A comparison
High pressure casting
Gate area is large, and the pressure inside the cavities is maintained at about 1 ton until the aluminum completely solidifies.
Directional Solidification
Because the gate area is large, pressure can be directed where it is required, thereby permitting directional solidification. (Final solidification occurs at the gate.)
Tilt-docking injection system
Due to our tilt-docking system, the time lapse from pouring to injection is shortened to the minimum, making it possible to maintain the temperature of the molten metal while achieving extra-slow injection.
Temperature distribution inside shot sleeve
The vertical shot sleeve maintains the temperature of the molten metal more than a horizontal sleeve, so the mold can be filled at an extremely slow rate.
Cavity comparison
The difference in the amount of retained gas indicates the big difference in the cavities.
Major uses for squeeze castings