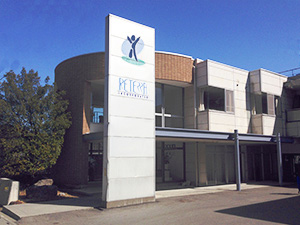
Ryokami Headquarters
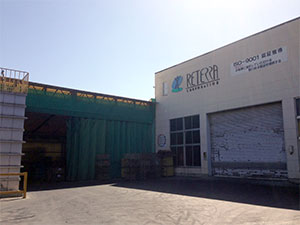
Ryokami Plant
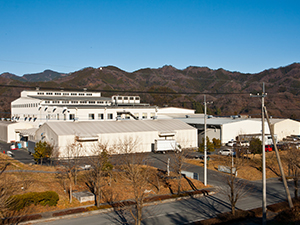
Chichibu Plant
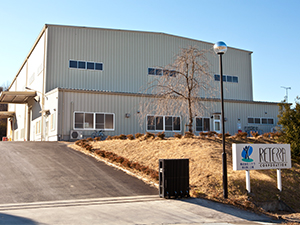
Chichibu Plant II
- Name of Corporation:
- Reterra Inc.
- Address
- Ryokami Headquarters [map showing location]
2703 Ryokamisusuki, Ogano-machi, Chichibu-gun, Saitama Prefecture 368-0201, Japan - Production Facilities:
- Ryokami Plant [map showing location]
2703 Ryokamisusuki, Ogano-machi, Chichibu-gun, Saitama Prefecture 368-0201, Japan
Chichibu Plant [map showing location]
9 Midorigaoka, Chichibu-city, Saitama Prefecture 368-0067, Japan
Chichibu Plant II [map showing location]
29-2 Midorigaoka, Chichibu-city, Saitama Prefecture 368-0067, Japan
- Foundation
- March 1977[click to see timeline]
- Representative
- Hiroyuki Akiyama, Representative Director and President
- Capital
- 90 million yen
- Shareholders
- F-TECH INC. (85%; listed on the First Section of the Tokyo Stock Exchange), UBE MACHINERY CORPORATION, LTD. (10%), and ALCONIX Corporation (5%; listed on the First Section of the Tokyo Stock Exchange)
- Number of Employees:
- 236 (as of April 1, 2022)
- Sales
- 3,944,000,000 yen (for fiscal year ending March 2021)
- Main business
- Manufacture and sale of aluminum and zinc castings
- Main customers
- Aisin Co., ; AISIN KEIKINZOKU Co. Ltd.;ALCONIX CORPORATION; Bosch Corporation; F-TECH INC.; GKN Driveline Japan Ltd.; Hitachi Astemo, Ltd.; Komatsu Ltd.; Knorr-Bremse Commercial Vehicle Systems Japan Ltd.; KYB Corporation; MITSUBISHI FUSO TRUCK & BUS CORPORATION; NEC Corporation; SUZUKI MOTOR CORPORATION
(in alphabetical order; capital letters according to company preference)